It is the nervous system of the whole vehicle electrical appliance that plays a vital role in the realization of the function of the whole vehicle electrical appliance. The electric safety of the whole vehicle has always been the most concerned issue of automobile manufacturers, and the working environment in each area may have an impact on the Wiring Harness. Waterproofing is a content that can't be ignored in the Wire Harness design. Therefore, this paper will briefly analyze the waterproofing design of the wiring harness. 1 Distribution of Wet and Dry Areas of The Whole Vehicle The vehicle wading depth refers to the deepest water area that the vehicle can pass through, and it is also a safe depth. The areas below the wading line and the engine compartment are called wet areas, while the areas where the electric wire bundles installed in the cab, passenger compartment and luggage compartment do not need special waterproof protection are called dry areas. In order to improve the wading ability and safety of the whole vehicle, the wading depth of the whole vehicle should be fully considered when designing the electrical system, and the key electrical components of the whole vehicle should be arranged in the dry area. 2 Wiring Harness Arrangement According to the distribution of the wet and dry areas of the whole vehicle, we divide the vehicle harness into the following parts: front cabin harness, powertrain harness, instrument harness, indoor harness, ceiling harness, four-door harness and back door harness. According to the distribution of the wet and dry areas of the whole vehicle, the front cabin harness, the powertrain harness and the four-door harness are located in the wet area, so this part of the money harness needs to be waterproof and protected, and the part connected to the room should be sealed with rubber parts. The rest of the harness is located in the dry area, and the Connector does not need to be waterproof. However, when connecting with the outside world, corresponding waterproof treatment should be done to prevent water from entering the room. 3 Waterproof Design of Wire Harness 3.1 Wire Harness Winding Method There are four winding methods for the whole vehicle harness: semi-package winding, coarse winding, double winding and 2/3 package winding. Among them, the whole vehicle wiring harness mostly adopts semi-enclosed winding method or coarse winding method, so-called semi-enclosed winding method and bundling wires into a bundle. The width of insulating tape is about 1/2 times that of winding, and it is required that the middle wire cannot be seen and the adhesive surface of insulating tape is not exposed; The rough winding rule is to bundle the wires into a bundle, and the spacing width of the insulating tape is 0 to 1.5 times the width of the tape, so that the adhesive surface of the insulating tape is not exposed. The front cabin wiring harness and powertrain wiring harness are in direct contact with the outside world, so special waterproof treatment is required, and the wiring harness is required to adopt semi-encapsulation winding method; Under the working condition of rain or car washing, the door harness has a high probability of coming into contact with water. Therefore, the door harness also needs special waterproof treatment, and it is required to adopt semi-package winding method to prevent the short circuit caused by water stopping into the harness from affecting the safety of the whole vehicle. For the wiring harness that needs special waterproof treatment, the branches of the wiring harness should be cross-wound, and the wiring harness should not be exposed. In the area where waterproof aprons and through-hole rubber sleeves are added, it is required that the wire harness be semi-wrapped first, and then the rubber rings or rubber sleeves and the wire harness be double-wound. As wiring harness winding is very important for waterproofing, wiring harness manufacturers must be required to wind it as required to ensure the safety of the whole vehicle. 3.2 Selection of Waterproof Connector The connector of the whole vehicle has two main functions. First, it can realize the docking with electrical devices, ensure the reliability of signal transmission, ensure insulation and prevent short circuit at the same time; Secondly, the connector itself has a positioning clip, which can prevent the connector from moving. In principle, the connector in the cab should be waterproof, for example, the connector in the engine compartment should be waterproof rubber sealing plug. Due to the influence of sealing, the waterproof connector will generate heat at the contact point when working, resulting in temperature rise. It is generally believed that the working temperature of the waterproof connector is equal to the sum of the ambient temperature and the temperature rise of the contact point. Therefore, when selecting waterproof connector, its temperature resistance should be taken into account. 3.3 Sealing Including sealed wiring harness interconnection point, grounding point and via hole protection. Due to the siphon phenomenon, the internal temperature of the electrical module will rise when it works, and it will gradually drop when it stops working, resulting in the reduction of internal pressure. Water seeps into the wiring harness from the place where the seal is not lax, and seeps into the electrical module along the gap between multiple copper wires under the action of pressure difference, resulting in the failure of the electrical module. Besides waterproof connectors, it is necessary to seal the interconnection points and grounding points of the wiring harness. The most common way is to seal the wiring harness with adhesive heat shrinkable tube. When the wire harness needs to pass through the sheet metal hole of the car body, a rubber protective sleeve must be added for protection. It is suggested that the hole larger than 40mm should be flanged to protect the wire harness, waterproof and seal. Generally, there are two kinds of via holes, one is a simple gold-muting hole, which does not involve moving parts. At this time, attention should be paid to the relative positions of the wire harnesses before and after the via hole, and the height of the outdoor wire harness is required to be lower than that of the indoor wire harness; When moving parts are involved, the design of rubber parts and interfaces should be fully considered. On the premise of ensuring that there is no interference and friction in the moving process, the sealing of rubber parts and the relative position of hole diameter should be considered, and the outdoor hole should be lower than the sheet metal hole in the connecting room as far as possible. 3.4 Harness Layout Protection The most important point of electrical system water inflow is that water seeps into the electrical system by its own gravity. Besides conventional waterproof materials for protection, reasonable three-dimensional layout can also achieve waterproof function. First of all, the grounding of the whole vehicle is a weak link in waterproofing, which is easy for water to seep into the electrical system. Therefore, from the early stage of design, we should fully consider the layout of the electrical appliances of the whole vehicle. The installation point of the electrical appliances should be higher than the grounding point, and the installation direction of the grounding harness should be downward, so that the problem of water seepage caused by the gravity of water can be effectively solved by optimizing the installation position. Secondly, the wiring harness that is close to the drainage point of the whole vehicle, such as the door wiring harness and the rear protection wiring harness, is arranged. Because rainwater will drip on the wiring harness, some wiring harnesses need to fix their directions and set the lowest point, so that the water dripping on the wiring harness will flow outside the vehicle by relying on the wiring harness, thus achieving the purpose of protecting the electrical system. 4 Concluding remarks With the rapid development of automotive electronics, the electric power of the whole vehicle is increasing day by day, and the safety and stability of the whole vehicle become more and more important. As the safety design of the nervous system harness of the whole vehicle, we Kable-X should not only rely on traditional technologies, but also constantly explore and learn new technologies.
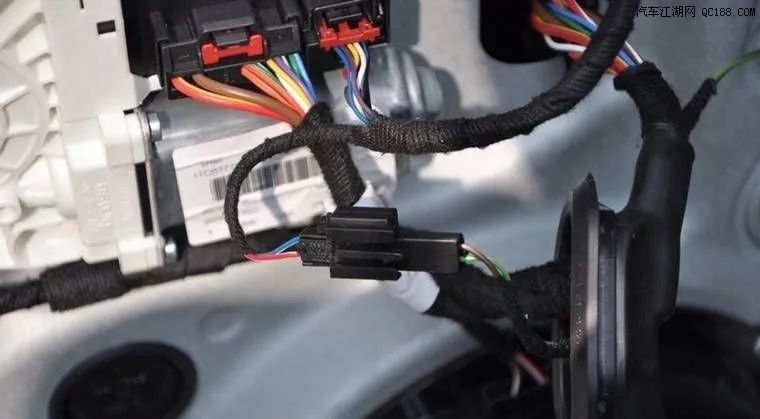